Kuinka korkean tarkkuuden osat koneistetaan
2023-09-22
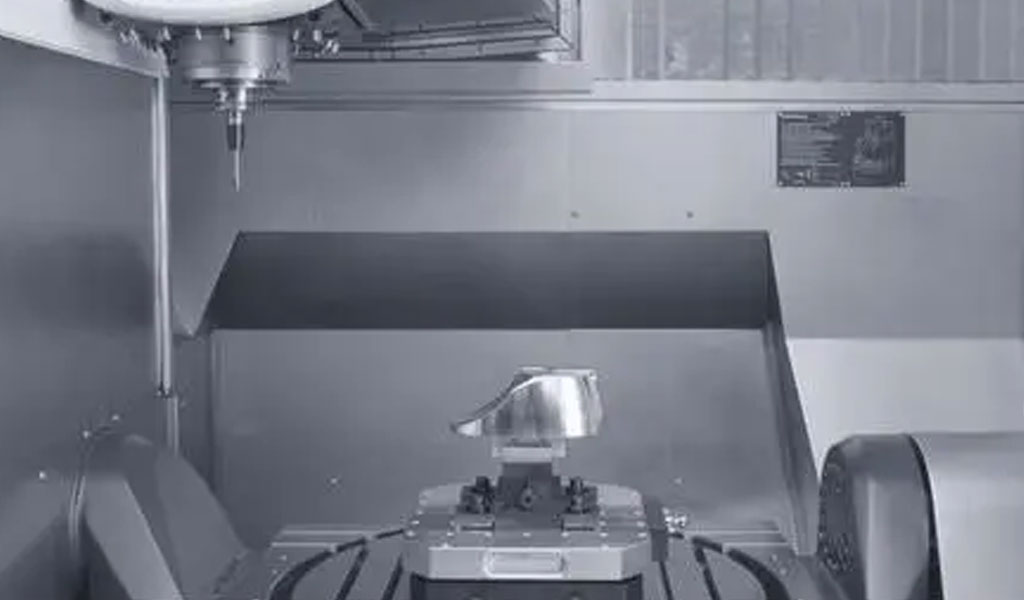
Tarkkuuskoneistuksen ymmärtäminen
Tarkkuuskoneistus on nykyaikaisen valmistuksen kulmakivi, joka vastaa monimutkaisten ja tarkkojen komponenttien tuotannosta, joita käytetään monilla eri aloilla. Ymmärtääksemme sen merkityksen täysin, tutkitaan tarkkuuskoneistuksen ydinkäsitteitä, sen tärkeää roolia eri sektoreilla ja historiallista matkaa, joka on johtanut sen nykyiseen huipputasoon.A. Mitä on tarkkuuskoneistus?
Tarkkuustyöstyksellä tarkoitetaan sarjaa valmistusprosesseja, jotka poistavat materiaalia työkappaleesta erittäin tarkasti ja tarkasti, mikä johtaa hienosti muotoiltuihin komponentteihin, joilla on tiukat toleranssit. Tämä prosessi muuntaa raaka-aineet, kuten metallit, muovit tai keramiikka, tarkkoja osia, jotka täyttävät tiukat vaatimukset. Tarkkuuskoneistuksen tärkeimmät ominaisuudet ovat:- tarkkuus: Tarkkuustyöstyksellä varmistetaan, että lopputuote on tarkasti suunniteltu suunnitelman mukainen minimaalisella poikkeamalla.
- Tiukat toleranssit: Se mahdollistaa osien valmistuksen erittäin tiukoilla toleransseilla, mikä tarkoittaa, että valmiit komponentit noudattavat tarkasti määritettyjä mittoja.
- Ylivoimainen pintakäsittely: Tarkkuustyöstö tarjoaa poikkeuksellisen pinnanlaadun, mikä usein eliminoi ylimääräisten viimeistelyprosessien tarpeen.
- Monimutkaiset geometriat: Se voi luoda monimutkaisia muotoja, ääriviivoja ja piirteitä, mikä tekee siitä välttämättömän monimutkaisten komponenttien valmistuksessa.
- Toistettavuus: Tarkkuus työstöprosessine ovat erittäin toistettavissa, mikä varmistaa tasaisen laadun useissa osissa.
- Monipuolisuus: Sitä voidaan soveltaa monenlaisiin materiaaleihin, joten se sopii useille eri aloille.
B. Tarkkuuskoneistuksen merkitys
Tarkkuustyöstyksellä on valtava merkitys useilla kriittisillä teollisuudenaloilla, ja se vaikuttaa jokapäiväisen elämämme eri puoliin. Tässä on joitain painavia syitä sen tärkeyteen:- Ilmailuteollisuus: Ilmailu- ja avaruusalalla tarkkuustyöstö on välttämätön ääriolosuhteita kestävien komponenttien valmistuksessa. Lentokoneiden moottorit, laskeutuminen vaihde, ja rakenneosat turvallisuuden ja suorituskyvyn takaavat tarkkuustyöstettyjen osien.
- Lääketieteelliset laitteet: Lääketieteelliset laitteet, kuten kirurgiset instrumentit, proteesit ja implantoitavat laitteet, vaativat tarkkaa työstöä biologisen yhteensopivuuden, tarkkuuden ja potilasturvallisuuden vuoksi.
- Autoteollisuus: Tarkkuuskoneistetut osat ovat välttämättömiä autoteollisuudelle ajoneuvojen luotettavuuden ja tehokkuuden varmistamiseksi. Komponentit, kuten moottorin osat, voimansiirtojärjestelmät ja jarrumekanismit, edellyttävät tarkkaa koneistusta.
- Elektroniikka ja puolijohteet: Tarkkuustyöstö on avainasemassa mikroelektronisten komponenttien ja puolijohdelaitteiden tuotannossa, jossa pienet toleranssit ovat välttämättömiä toimivuuden kannalta.
- Energia-ala: Energiateollisuus luottaa tarkkuuskoneistukseen sähköntuotannossa käytettävien kriittisten osien, mukaan lukien turbiinien, generaattoreiden ja voimansiirtokomponenttien, tuotannossa.
- Työkalujen ja meistien valmistus: Tarkkuustyöstö on ratkaisevan tärkeää työkalujen ja meistien valmistuksessa, joita puolestaan käytetään lukemattomien muiden tuotteiden valmistukseen.
- Consumer Electronics: Älypuhelimien, kannettavien tietokoneiden ja muun kulutuselektroniikan tuotannossa hyödynnetään tarkkaa koneistusta, joka varmistaa tyylikkään suunnittelun ja optimaalisen toiminnallisuuden.
- Tutkimus ja kehitys: Tutkijat ja tiedemiehet ovat riippuvaisia tarkkuuskoneistetuista komponenteista kokeissa, prototyypeissä ja laboratoriolaitteistoissa.
C. Historiallinen näkökulma
Tarkkuuskoneistuksen matka juontaa juurensa muinaisiin sivilisaatioihin, jolloin taitavat käsityöläiset käyttivät alkeellisia työkaluja materiaalien muotoiluun. Tuolloin saavutettu tarkkuus oli kuitenkin rajallista nykystandardeihin verrattuna.- Varhainen tarkkuuskoneistus: Teollinen vallankumous 18- ja 19-luvuilla merkitsi keskeistä ajanjaksoa tarkkuuskoneistuksen kehityksessä. Työstökoneiden, kuten sorvien ja jyrsinkoneiden, keksintö mullisti valmistuksen mahdollistamalla suuremman tarkkuuden ja johdonmukaisuuden.
- World War II: Tarkkuuskoneistuksella oli keskeinen rooli toisessa maailmansodassa, koska se oli välttämätöntä sotilasvarusteiden valmistuksessa vaaditulla tarkkuudella ja yhtenäisyydellä. Tämä aikakausi oli todistamassa edistystä koneistustekniikoissa ja uusien materiaalien ilmaantumista.
- Sodan jälkeiset edistysaskeleet: Sodan jälkeisellä kaudella teknologiset innovaatiot lisääntyivät, mukaan lukien tietokoneiden numeeristen ohjauskoneiden (CNC) käyttö. CNC-koneistus mahdollistavat automatisoidut ja erittäin tarkat toiminnot, mikä aloitti tuotannon uuden aikakauden.
- Digitaalinen aikakausi: Tietokoneiden ja ohjelmistojen integrointi koneistusprosesseihin on lisännyt tarkkuustyöstöä entisestään. Nykyaikaiset CNC-koneet voivat suorittaa monimutkaisia operaatioita vertaansa vailla olevalla tarkkuudella, mikä tekee niistä välttämättömiä nykypäivän tuotantoympäristössä.
Materiaalit ja niiden merkitys
Materiaalit ovat tarkkuuskoneistuksen perusta, ja oikean materiaalin valinnalla on keskeinen rooli tarkkuusosien valmistuksessa. Tässä osiossa perehdymme sopivien materiaalien valinnan tärkeyteen, ymmärrämme materiaalien ominaisuuksien merkityksen ja tutkimme erilaisia työstettävyyteen vaikuttavia tekijöitä.A. Materiaalien valinta
Tarkkuuskoneistuksen materiaalien valinta on kriittinen päätös, joka vaikuttaa suoraan lopputuotteen suorituskykyyn, kestävyyteen ja toimivuuteen. Valmistajien on otettava huomioon useita tekijöitä valitessaan materiaaleja:- Materiaalin soveltuvuus: Materiaalin tulee olla sopiva käyttötarkoitukseen. Eri toimialoilla ja sovelluksilla on erilaisia vaatimuksia, kuten lämpötilan kestävyys, korroosionkestävyys ja sähkönjohtavuus.
- Mekaaniset ominaisuudet: Mekaaniset ominaisuudet, kuten vetolujuus, kovuus ja sitkeys, ovat ratkaisevia. Esimerkiksi ilmailuteollisuudessa korkean vetolujuuden omaavia materiaaleja suositellaan rakenneosiksi.
- Lämpöominaisuudet: Jotkut sovellukset vaativat materiaaleja, joilla on erinomainen lämmönjohtavuus tai kestävyys korkeita lämpötiloja vastaan. Tämä on erityisen tärkeää sellaisilla aloilla kuin sähköntuotanto ja elektroniikka.
- Korroosionkestävyys: Ympäristöissä, joissa korroosio on huolenaihe, suositaan materiaaleja, jotka kestävät hyvin korroosiota, kuten ruostumaton teräs tai titaani.
- Painon huomioitavaa: Autoteollisuudessa ja ilmailuteollisuudessa usein etusijalle asetetaan kevyet materiaalit, kuten alumiini- tai hiilikuitukomposiitit vähentääkseen polttoaineenkulutusta ja parantaakseen suorituskykyä.
- Kustannusrajoitukset: Kustannukset ovat merkittävä tekijä materiaalin valinnassa. Suorituskykyiset materiaalit voivat olla kalliita, joten valmistajien on löydettävä tasapaino suorituskyvyn ja kustannustehokkuuden välillä.
- Sääntelyn noudattaminen: Terveydenhuollon kaltaisilla aloilla materiaalien on täytettävä tiukat bioyhteensopivuutta ja turvallisuutta koskevat normit.
- Saatavuus: Myös materiaalien saatavuus ja niiden lähteet vaikuttavat valintaan. Joillakin erikoisseoksilla tai komposiiteilla saattaa olla rajoitettu saatavuus.
B. Materiaalin ominaisuudet
Materiaalien ominaisuuksien ymmärtäminen on erittäin tärkeää tarkkuustyöstössä. Tässä on joitain tärkeimpiä materiaalin ominaisuuksia ja niiden merkitystä:- Vetolujuus: Vetolujuus mittaa materiaalin kykyä kestää vetovoimaa rikkoutumatta. Se on välttämätön rakenneosille ja mekaaniselle rasitukselle altistuville osille.
- Kovuus: Kovuus osoittaa materiaalin muodonmuutos- ja kulumiskestävyyden. Kovat materiaalit sopivat leikkaustyökaluihin, kun taas pehmeämmät materiaalit voivat olla suositeltavia tietyissä sovelluksissa, kuten tiivisteissä.
- sitkeys: Mutavuus viittaa materiaalin kykyyn muuttaa muotoaan murtumatta, kun se altistetaan vetojännitykselle. Muovattavat materiaalit ovat helpompia muotoilla, mutta ne eivät välttämättä sovellu sovelluksiin, jotka vaativat jäykkyyttä.
- Lämmönjohtokyky: Materiaalit, joilla on korkea lämmönjohtavuus, haihduttavat lämpöä tehokkaasti. Tämä ominaisuus on elintärkeä sovelluksissa, joissa lämpötilan hallinta on kriittinen.
- Sähkönjohtavuus: Sähkönjohtavuus on välttämätöntä elektroniikassa ja sähkökomponenteissa, joissa materiaalien on helpotettava sähkön virtausta.
- Magneettiset ominaisuudet: Magneettiset ominaisuudet ovat merkittäviä sellaisilla aloilla, kuten sähkömagneettinen ja elektroniikka, joissa materiaalien on ehkä oltava ferromagneettisia tai ei-magneettisia.
- Kemiallinen resistanssi: Materiaalien on kestettävä kemiallista korroosiota ympäristöissä, joissa ne altistuvat hapoille, emäksille tai muille syövyttäville aineille.
C. Koneistettavuustekijät
Koneistettavuus viittaa siihen, kuinka helposti materiaalia voidaan työstää, leikata tai muotoilla. Siihen vaikuttavat useat tekijät, mukaan lukien:- Materiaalin kovuus: Pehmeämpiä materiaaleja on yleensä helpompi työstää, kun taas kovemmat materiaalit saattavat vaatia erikoistyökaluja ja -tekniikoita.
- Sirun muodostuminen: Lastujen muodostuminen ja poistuminen koneistuksen aikana vaikuttavat prosessin tehokkuuteen ja pinnan viimeistelyyn.
- Työkalujen kuluminen: Eri materiaalit voivat aiheuttaa eriasteista työkalun kulumista, mikä vaikuttaa koneistusnopeuteen ja -kustannuksiin.
- Jäähdytysneste ja voitelu: Oikea jäähdytysneste ja voitelu ovat välttämättömiä kitkan, lämmön ja työkalun kulumisen vähentämiseksi koneistuksen aikana.
- Leikkausnopeus: Nopeus, jolla leikkaustyökalu liikkuu materiaalin läpi, vaikuttaa sekä tuottavuuteen että koneistetun pinnan laatuun.
- Työkalun materiaali: Leikkuutyökalun materiaalin valinta, kuten kovametalli tai pikateräs, riippuu koneistettavasta materiaalista.
- Leikkausparametrit: Leikkausparametrien, kuten syöttönopeuden ja leikkaussyvyyden, säätäminen voi optimoida työstöprosessin tietyille materiaaleille.
Työstökoneet tarkkuuskoneistukseen
Työstökoneet ovat tarkkuuskoneistuksen sydän, mikä mahdollistaa raaka-aineiden muuttamisen erittäin tarkkoiksi osiksi. Tässä osiossa tutkimme neljää avaintyyppiä tarkkuuskoneistuksessa käytettyjä työstökoneita: CNC-työstökeskukset, sorvauskoneet, hiomakoneet ja EDM (Electrical Discharge Machining). Jokaisella näistä koneista on ainutlaatuinen rooli tarkkojen komponenttien tuotannossa.A. CNC-työstökeskukset
CNC-työstökeskukset (Computer Numerical Control) ovat monipuolisia ja niitä käytetään laajalti tarkkuustyöstyksessä. Ne ovat automatisoituja järjestelmiä, jotka ohjaavat leikkuutyökalujen ja työkappaleiden liikettä poikkeuksellisen tarkasti. Tässä on yleiskatsaus CNC-työstökeskuksista ja niiden merkityksestä:- Monipuolisuus: CNC-työstökeskukset voivat suorittaa erilaisia työstötoimenpiteitä, mukaan lukien jyrsintä, poraus ja kierre. Tämä monipuolisuus mahdollistaa monimutkaisten osien valmistamisen, joissa on useita ominaisuuksia.
- high Precision: CNC-koneiden tietokoneistettu ohjaus varmistaa työkalujen tarkan paikantamisen ja tasaisen tuloksen, mikä tekee niistä ihanteellisia osille, joilla on tiukat toleranssit.
- Automaatio: CNC-työstökeskukset voivat toimia jatkuvasti ilman ihmisen puuttumista. Tämä automaatio lisää tehokkuutta ja vähentää virheiden riskiä.
- Monimutkaiset geometriat: Ne ovat erinomaisia monimutkaisten muotojen ja ääriviivojen työstämisessä, mikä tekee niistä sopivia teollisuudelle, kuten ilmailuteollisuudelle, jossa monimutkaiset komponentit ovat yleisiä.
- Toistettavat tulokset: CNC-koneet tarjoavat erinomaisen toistettavuuden, mikä varmistaa, että jokainen valmistettu osa vastaa suunnittelun tarkkoja vaatimuksia.
- Lyhennetyt asennusajat: CNC-työstökeskukset voidaan ohjelmoida siirtymään nopeasti eri tehtävien välillä, minimoiden asennusajat ja lisäämään tuotannon tehokkuutta.
B. Sorvauskoneet
Sorvauskoneita käytetään sylinterimäisten osien luomiseen pyörittämällä työkappaletta samalla kun leikkaustyökalu poistaa materiaalia sen ulkopinnalta. Ne ovat välttämättömiä tuotannossa akselis, tapit ja muut komponentit, joilla on pyörimissymmetria. Sorvauskoneiden tärkeimpiä kohtia ovat:- Sylinterimäiset osat: Sorvauskoneet ovat erikoistuneet tuottamaan lieriömäisiä tai putkimaisia osia, mukaan lukien kierteiset tai monimutkaiset urat.
- Suuret nopeudet: Ne toimivat suurilla nopeuksilla, joten ne sopivat osiin, jotka vaativat sileän ja tarkan viimeistelyn.
- Yhden akselin toiminta: Useimmat sorvauskoneet ovat yksiakselisia, ja ne keskittyvät työkappaleen ulkopinnan muotoiluun.
- Tehokas massatuotantoon: Sorvaus on erittäin tehokasta massatuotantoon osissa, joissa materiaalihukkaa on vähän.
- Sorvikoneet: Manuaaliset ja CNC-ohjatut sorvikoneet ovat yleisesti käytettyjä sorvauskoneita, jotka tarjoavat erilaisia ominaisuuksia.
C. Hiomakoneet
Hiomakoneet on suunniteltu kovien tai hankaavien materiaalien tarkkuuspintojen viimeistelyyn ja muotoiluun. Ne ovat tärkeitä äärimmäisen tiukkojen toleranssien ja erinomaisen pintakäsittelyn saavuttamiseksi. Tästä syystä hiomakoneet ovat tärkeitä:- Mikronitason tarkkuus: Hiomakoneet voivat saavuttaa mikronitason tarkkuuden, joten ne ovat välttämättömiä sovelluksissa, jotka vaativat korkeinta tarkkuutta.
- Materiaalin poisto: Ne poistavat materiaalia hankaamalla, mikä mahdollistaa pinnan epätasaisuuksien korjaamisen ja poikkeuksellisen sileyden.
- Työkalun ja leikkurin hionta: Pintahionnan lisäksi on olemassa erikoishiomakoneita leikkaustyökalujen teroittamiseen ja tarkkojen profiilien tuottamiseen.
- Erilaisia hiontamenetelmiä: Erityyppiset hiomakoneet, mukaan lukien pintahiomakoneet, sylinterimäiset hiomakoneet ja keskittömät hiomakoneet, vastaavat erilaisiin työstötarpeisiin.
- Karkaistut materiaalit: Hionta soveltuu erityisen hyvin karkaistuille materiaaleille, kuten työkaluteräs ja keramiikka, joissa perinteiset työstömenetelmät voivat olla tehottomia.
D. EDM (sähköpurkauskoneistus)
EDM tai Electrical Discharge Machining on ei-perinteinen työstöprosessi, joka käyttää sähköpurkauksia materiaalien muotoiluun. Se on ihanteellinen monimutkaisten ja herkkien osien luomiseen, joissa perinteiset leikkaustyökalut voivat vahingoittaa. EDM:n tärkeimmät osat ovat:- Ei fyysistä kontaktia: EDM ei sisällä suoraa fyysistä kosketusta työkalun ja työkappaleen välillä, mikä minimoi työkalun kulumisen ja herkkien materiaalien vaurioitumisen riskin.
- high Precision: Se voi saavuttaa korkean tarkkuuden ja pinnanlaadun jopa poikkeuksellisen kovilla materiaaleilla.
- Wire EDM ja Sinker EDM: EDM-koneita on kahta päätyyppiä: langan leikkaus EDM, joka käyttää lankaelektrodia, ja uppo-EDM, joka käyttää muotoiltua elektrodia.
- Monimutkaiset muodot: EDM voi tuottaa monimutkaisia muotoja, kuten muotteja ja muotteja, joissa on monimutkaisia yksityiskohtia ja hienoja ominaisuuksia.
- Lämmön vaikutusalue: Koska EDM ei tuota lämpöä työkappaleeseen, se soveltuu lämpöherkille materiaaleille, kuten ilmailu- ja avaruusseoksille.
- Hidas prosessi: EDM on suhteellisen hidasta muihin koneistusmenetelmiin verrattuna, joten se soveltuu parhaiten pienikokoisiin ja erittäin tarkkoihin töihin.
Leikkaustyökalut ja työkalut
Leikkaustyökalut ovat tarkkuuskoneistuksen eturintamassa, ja ne toimivat työkaluina, jotka muotoilevat ja muuntavat raaka-aineita erittäin tarkkoiksi osiksi. Tässä osiossa tutkimme erilaisia leikkaustyökaluja, työkalujen pinnoitteiden merkitystä sekä työkalun käyttöikään ja kulumiseen vaikuttavia tekijöitä.A. Leikkuutyökalujen tyypit
Tarkkuustyöstö perustuu erilaisiin leikkaustyökaluihin, joista jokainen on suunniteltu tiettyihin tehtäviin ja materiaaleihin. Leikkuutyökalun valinta vaikuttaa suuresti koneistusprosessin tehokkuuteen ja tarkkuuteen. Tässä on joitain yleisiä leikkaustyökalutyyppejä:- Loppumyllyt: Päätyjyrsimet ovat monipuolisia työkaluja, joita käytetään jyrsintään. Niissä on useita leikkausreunoja, ja ne voivat poistaa materiaalia työkappaleesta useilla tavoilla, mukaan lukien pinnat, ääriviivat ja urat.
- Porat: Porat on suunniteltu reikien tekemiseen työkappaleisiin. Niitä on eri muodoissa, mukaan lukien kierreporat, keskiporat ja kääntöporat.
- Lisäyslistojen kääntäminen: Näitä käytetään sorvauskoneissa lieriömäisten osien muotoiluun. Sorvausteriä on saatavana useissa eri muodoissa ja materiaaleissa eri käyttötarkoituksiin.
- Jyrsinkoneet: Jyrsimiä on eri muotoisia, kuten tasojyrsimiä, kuulajyrsimiä ja urajyrsimiä, ja niitä käytetään jyrsinkoneissa luomaan erilaisia ominaisuuksia työkappaleeseen.
- Kalvaimet: Kalvikkeita käytetään aiemmin porattujen reikien viimeistelyyn ja mitoittamiseen tarkkoihin mittoihin. Ne takaavat tasaiset ja tarkat reikäpinnat.
- Hanat ja kuopat: Näitä leikkaustyökaluja käytetään kierteittämiseen. Tapit luovat sisäkierteet, kun taas meistit luovat ulkoiset kierteet.
- Hiomalaikat: Hiomalaikat ovat hiomatyökaluja, joita käytetään pinnan tarkkuushiontaan. Niitä on saatavana erilaisina hiomamateriaaleina ja karkeuskokoina.
- Avartimet: Aventimet ovat erikoistyökaluja, joita käytetään sisäisten ja ulkoisten muotojen ja profiilien, kuten kiilaurien ja urien leikkaamiseen.
- Vastaporat ja upottimet: Näitä työkaluja käytetään luomaan syvennyksiä tai viisteitä reikien ympärille kiinnikes.
- Tylsät baarit: Poraustankoja käytetään porausoperaatioissa olemassa olevien reikien suurentamiseen tarkasti.
B. Työkalujen pinnoitteet
Työkalupinnoitteet ovat ohuita materiaalikerroksia, jotka levitetään leikkuutyökaluihin niiden suorituskyvyn ja kestävyyden parantamiseksi. Näillä pinnoitteilla on useita etuja:- Vähentynyt kitka: Pinnoitteet, kuten titaaninitridi (TiN) ja titaanikarbonitridi (TiCN), vähentävät kitkaa työkalun ja työkappaleen välillä, mikä johtaa tasaisempaan leikkaamiseen ja pidentäen työkalun käyttöikää.
- Tehostettu kovuus: Pinnoitteet lisäävät työkalun pinnan kovuutta tehden siitä kestävämmän kulumista ja pidentäen työkalun käyttöikää.
- Parempi lämmönkestävyys: Pinnoitteet kestävät työstön aikana syntyviä korkeita lämpötiloja, mikä vähentää lämmöstä johtuvaa työkalun kulumista ja lisää leikkausnopeuksia.
- Rakentamisen estävät ominaisuudet: Joillakin pinnoitteilla on tarttumista estäviä ominaisuuksia, jotka estävät materiaalin kerääntymisen työkalun leikkuureunoihin.
- Lisääntynyt voitelukyky: Pinnoitettujen työkalujen voitelu on parantunut, mikä vähentää liiallisen jäähdytysnesteen tarvetta ja tehostaa lastujen poistumista.
C. Työkalun käyttöikä ja kuluminen
Työkalun käyttöiän ja kulumisen ymmärtäminen on ratkaisevan tärkeää koneistusprosessien optimoimiseksi ja tuotantokustannusten minimoimiseksi. Työkalun käyttöikä viittaa siihen, kuinka kauan leikkaustyökalu pysyy tehokkaana ennen kuin se on vaihdettava tai kunnostettava. Useat tekijät vaikuttavat työkalun käyttöikään ja kulumiseen:- Leikkausnopeus: Suuremmat leikkausnopeudet voivat lisätä työkalun kulumista koneistuksen aikana syntyvien korkeampien lämpötilojen vuoksi. Oikea leikkausnopeuksien valinta on välttämätöntä työkalun käyttöiän ja tuottavuuden tasapainottamiseksi.
- Syöttöarvo: Nopeus, jolla leikkaustyökalu etenee työkappaleeseen, vaikuttaa työkalun kulumiseen. Suuret syöttönopeudet voivat nopeuttaa kulumista, kun taas pienemmät syöttönopeudet voivat pidentää työkalun käyttöikää.
- Leikkauksen syvyys: Leikkaussyvyys vaikuttaa poistettavan materiaalin määrään ajoa kohti. Syvemmät leikkaukset voivat lisätä työkalun kulumista, joten syvyyden optimointi on kriittistä.
- Materiaalin kovuus: Kovien materiaalien leikkaaminen voi nopeuttaa työkalun kulumista. Kovien materiaalien tehokkaaseen työstämiseen käytetään erikoistyökaluja ja pinnoitteita.
- Jäähdytysneste ja voitelu: Oikea jäähdytysneste ja voitelu auttavat haihduttamaan lämpöä ja vähentämään kitkaa, mikä pidentää työkalun käyttöikää.
- Työkalun materiaali: Materiaali, josta leikkuutyökalu on valmistettu, vaikuttaa sen kulutuskestävyyteen. Materiaalit, kuten kovametalli ja keramiikka, tarjoavat erinomaisen kulutuskestävyyden.
- Työkalun geometria: Leikkuutyökalun geometrialla, mukaan lukien kallistuskulma, kohotuskulma ja lastunmurtajan rakenne, on merkittävä rooli kulumiskuvioissa.
- Työkappaleen materiaali: Työstettävän materiaalin tyyppi vaikuttaa työkalun kulumiseen. Hankaavat materiaalit voivat johtaa työkalun nopeampaan kulumiseen.
Tarkkuustyöstöprosessit
Tarkkuustyöstöprosessit ovat menetelmiä, joilla raaka-aineet muunnetaan erittäin tarkkoiksi osiksi, joilla on tiukat toleranssit ja poikkeuksellinen pintakäsittely. Tässä osiossa tutkimme viittä tärkeintä tarkkuustyöstöprosessia: sorvaus, jyrsintä, poraus, hionta ja sähköpurkauskoneistus (EDM). Jokainen näistä prosesseista palvelee ainutlaatuista tarkoitusta ja niitä käytetään työkappaleen erityisvaatimusten perusteella.A. Kääntäminen
Sorvaus on koneistusprosessi, jota käytetään ensisijaisesti lieriömäisten osien muotoiluun. Siinä pyöritetään työkappaletta samalla kun yksikärkinen leikkaustyökalu poistaa materiaalia ulkopinnalta. Tässä ovat tärkeimmät käännökset:- Sylinterimäiset osat: Sorvaus on ihanteellinen lieriömäisten komponenttien, kuten akselien, tappien ja holkkien, valmistukseen.
- Pyörimissymmetria: Sopii hyvin pyörimissymmetriaa vaativiin osiin, koska työkappale pyörii sorvissa samalla kun leikkuutyökalu muotoilee sitä.
- Erilaisia operaatioita: Sorvaus voi suorittaa erilaisia toimintoja, mukaan lukien tasoitus, sorvaus (halkaisijan pienentäminen), kartiosorvaus ja kierretys.
- Yhden pisteen leikkaus: Yksi leikkaustyökalu poistaa materiaalia jatkuvalla liikkeellä, mikä johtaa tehokkaaseen materiaalin poistoon.
- Sorvikoneet: Sekä manuaalisia että CNC-ohjattuja sorveja käytetään yleisesti sorvaukseen.
B. Jyrsintä
Jyrsintä on monipuolinen tarkkuustyöstöprosessi, jossa käytetään monipisteleikkaustyökaluja materiaalin poistamiseen työkappaleesta. Se sopii hyvin monenlaisten muotojen ja ominaisuuksien luomiseen. Jyrsinnän tärkeimmät osat ovat:- Monipuolisuus: Jyrsintä voi tuottaa tasaisia pintoja, uria, taskuja ja monimutkaisia muotoja. Sitä käytetään sekä 2D- että 3D-koneistukseen.
- Monipisteleikkaus: Useat työkalun leikkuureunat ovat vuorovaikutuksessa työkappaleen kanssa samanaikaisesti, mikä mahdollistaa tehokkaan materiaalin poistamisen.
- Jyrsintätyypit: Jyrsintä voidaan suorittaa käyttämällä erilaisia jyrsimiä, mukaan lukien päätyjyrsimet, tasojyrsimet ja kuulajyrsimet.
- CNC -työstökeskukset: CNC-ohjatut jyrsinkoneet tarjoavat tarkan työkalun liikkeen hallinnan ja niitä käytetään laajasti nykyaikaisessa koneistuksessa.
- Suuret nopeudet: Jyrsintä voidaan suorittaa suurilla nopeuksilla, mikä mahdollistaa tehokkaan tuotannon.
C. Poraus
Poraus on tarkkuustyöstöprosessi, jota käytetään reikien tekemiseen työkappaleisiin. Se on perustoiminto eri toimialoilla. Porauksen tärkeimmät osat ovat:- Reikien luominen: Porakoneet käyttävät erikoistyökaluja, joita kutsutaan poraksi materiaalin poistamiseen ja tietyn halkaisijan omaavien reikien luomiseen.
- Poratyypit: Saatavilla on erityyppisiä poraa, mukaan lukien kierreporat, keskiporat ja kääntöporat, joista jokainen on suunniteltu tiettyihin sovelluksiin.
- tarkkuus: Tarkka asemointi ja kohdistus ovat välttämättömiä porauksessa, jotta voidaan varmistaa, että reiät luodaan tarkasti.
- Nopeus ja syöttönopeus: Porausparametrit, kuten pyörimisnopeus ja syöttönopeus, ovat kriittisiä haluttujen reiän mittojen saavuttamiseksi.
- Jäähdytysneste ja voitelu: Asianmukaista jäähdytysnestettä ja voitelua käytetään lämmön haihduttamiseen ja kitkan vähentämiseen porauksen aikana.
D. Hionta
Hionta on tarkkuustyöstöprosessi, jossa käytetään hiomalaikkoja materiaalin poistamiseen ja äärimmäisen tiukkojen toleranssien ja pinnan viimeistelyyn. Hionnan tärkeimmät osat ovat:- Poikkeuksellinen tarkkuus: Hionta voi saavuttaa mikronitason tarkkuuden, joten se on ihanteellinen sovelluksiin, jotka vaativat korkeinta tarkkuutta.
- Pinnan viimeistely: Se tuottaa erinomaisen pintakäsittelyn, mikä usein eliminoi ylimääräisten viimeistelyprosessien tarpeen.
- Tarvikkeet: Hionta soveltuu koville ja hankaaville materiaaleille, mukaan lukien karkaistu teräs, keramiikka ja kovametallit.
- Erilaisia hiontamenetelmiä: Erityyppiset hiomakoneet, kuten pintahiomakoneet, lieriömäiset hiomakoneet ja keskittömät hiomakoneet, vastaavat erilaisiin työstötarpeisiin.
- Jäähdytysneste: Oikea jäähdytysneste on välttämätöntä hionnassa ylikuumenemisen estämiseksi ja pyörän eheyden säilyttämiseksi.
E. Sähköpurkauskoneistus (EDM)
EDM eli Electrical Discharge Machining on ei-perinteinen tarkkuustyöstöprosessi, joka käyttää sähköpurkauksia materiaalin poistamiseen. Se soveltuu erityisesti monimutkaisten ja monimutkaisten muotojen sekä kovien ja kuumuutta kestävien materiaalien koneistukseen. EDM:n tärkeimmät osat ovat:- Kosketukseton koneistus: EDM ei sisällä suoraa kosketusta työkalun ja työkappaleen välillä, mikä vähentää työkalun kulumisen ja vaurioitumisen riskiä.
- high Precision: EDM voi saavuttaa suuren tarkkuuden, joten se sopii sovelluksiin, joissa tiukat toleranssit ovat välttämättömiä.
- Monimutkaiset muodot: Se on erinomainen monimutkaisten muotojen, meistien, muottien ja komponenttien työstämisessä hienoilla yksityiskohdilla.
- Wire EDM ja Sinker EDM: EDM-koneita on kahta päätyyppiä: lanka-EDM, joka käyttää lankaelektrodia, ja uppo-EDM, joka käyttää muotoiltua elektrodia.
- Hidas prosessi: EDM on suhteellisen hidasta muihin koneistusmenetelmiin verrattuna, joten se soveltuu parhaiten pienikokoisiin ja erittäin tarkkoihin töihin.
Toleranssit ja laadunvalvonta
Tarkkuustyöstö vaatii huolellista huomiota yksityiskohtiin ja tiukkaa sitoutumista laadunvalvontaan sen varmistamiseksi, että osat täyttävät määrätyt standardit. Tässä osiossa tutkimme kolmea tarkkuuskoneistuksen laadunvalvonnan kriittistä näkökohtaa: geometrinen mitoitus ja toleranssi (GD&T), tilastollinen prosessinohjaus (SPC) ja laadunvarmistus.A. Geometrinen mitoitus ja toleranssi (GD&T)
Geometrinen mitoitus ja toleranssi, usein lyhennettynä GD&T, on järjestelmä, jota käytetään määrittämään ja välittämään osan piirteiden koon, muodon, suunnan ja sijainnin sallitut vaihtelut. GD&T on elintärkeä tarkkuuskoneistuksessa seuraavista syistä:- Tarkkaa viestintää: GD&T tarjoaa standardoidun kielen insinööreille, suunnittelijoille ja koneistajille, jotka voivat viestiä suunnittelutarkoituksista ja mittavaatimuksista tarkasti.
- Toleranssin selvennys: Se auttaa määrittelemään kriittisten mittojen hyväksyttävän vaihtelun varmistaen, että kaikki sidosryhmät ymmärtävät sallitut poikkeamat.
- Parannettu laatu: GD&T edistää parempaa laatua vähentämällä epäselvyyttä suunnittelussa ja minimoimalla virheiden riskin koneistuksen aikana.
- Kustannustehokkuus: Selkeät GD&T-spesifikaatiot voivat johtaa alentuneisiin valmistuskustannuksiin, koska osia ei todennäköisesti romutetaan tai ne tarvitsevat uudelleenkäsittelyä väärinkäsityksen tai väärintulkintojen vuoksi.
- Monimutkainen geometria: Se on erityisen hyödyllinen osille, joilla on monimutkainen geometria, mikä varmistaa, että kaikki ominaisuudet valmistetaan haluttujen eritelmien mukaisesti.
B. Tilastollisen prosessin ohjaus (SPC)
Statistical Process Control (SPC) on laadunvalvontamenetelmä, joka käyttää tilastollisia tekniikoita koneistusprosessin valvontaan ja ohjaukseen. SPC on välttämätön tarkkuuskoneistuksessa seuraavista syistä:- Prosessin seuranta: SPC auttaa valvomaan koneistusprosesseja reaaliajassa ja tunnistamaan vaihtelut tai poikkeamat halutuista parametreista.
- Ongelmien varhainen havaitseminen: Prosessia jatkuvasti valvomalla SPC mahdollistaa sellaisten ongelmien varhaisen havaitsemisen, jotka voivat johtaa tekniseen poikkeaviin osiin, mikä vähentää hukkaa ja uudelleenkäsittelyä.
- Tietoihin perustuva päätöksenteko: SPC luottaa tietoihin ja tilastolliseen analyysiin tehdäkseen tietoisia päätöksiä prosessisäädöistä ja varmistaakseen, että koneistusprosessi pysyy hyväksyttävissä rajoissa.
- Parempi johdonmukaisuus: SPC edistää prosessin yhtenäisyyttä ja vähentää vaatimustenvastaisten osien muodostumisen todennäköisyyttä.
- Vähentynyt romu ja uusiotyö: Tunnistamalla ja korjaamalla prosessin vaihtelut nopeasti SPC minimoi viallisten osien tuotannon, mikä vähentää romu- ja korjauskustannuksia.
C. Tarkkuuskoneistuksen laadunvarmistus
Tarkkuuskoneistuksen laadunvarmistus sisältää kattavan lähestymistavan sen varmistamiseen, että valmistetut osat täyttävät tai ylittävät määritetyt laatustandardit. Se sisältää erilaisia elementtejä, mukaan lukien:- Prosessin dokumentaatio: Yksityiskohtainen työstöprosessien dokumentaatio, mukaan lukien vakiokäyttömenettelyt (SOP) ja työohjeet, varmistaa, että jokainen vaihe suoritetaan johdonmukaisesti.
- Tarkastus ja mittaus: Tarkka tarkastus ja mittaus tarkkuusinstrumenteilla ja metrologisilla tekniikoilla varmistaa, että osat ovat määritettyjen toleranssien ja laatustandardien mukaisia.
- Kalibrointi: Työstölaitteiden ja mittauslaitteiden säännöllinen kalibrointi on välttämätöntä tarkkuuden ja jäljitettävyyden ylläpitämiseksi.
- Materiaalin tarkastus: Materiaalien ominaisuuksien, koostumuksen ja laadun tarkistaminen on ratkaisevan tärkeää sen varmistamiseksi, että käytetty materiaali täyttää suunnitteluvaatimukset.
- Työntekijän koulutus: Koneistajille ja laadunvalvontahenkilöstölle suunnatut koulutus- ja taitojen kehittämisohjelmat varmistavat, että he ovat taitavia tehtävissään ja vastuissaan.
- Perussyyanalyysimenetelmiä: Kun vaatimustenvastaisia osia havaitaan, syyanalyysi suoritetaan ongelman lähteen määrittämiseksi ja korjaavien toimien toteuttamiseksi.
- Jatkuva parantaminen: Jatkuvan parantamisen kulttuuri edistää innovointia ja ajaa jatkuvia parannuksia koneistusprosesseissa ja laadunvalvontamenettelyissä.
- Asiakaspalaute: Asiakaspalautteen kerääminen ja analysointi auttaa tunnistamaan kehittämiskohteita ja sovittamaan koneistusprosessit asiakkaiden odotuksiin.
Yhteenveto
A. Tarkkuuskoneistuksen taide ja tiede
Tarkkuuskoneistus on taiteen ja tieteen risteyksessä, jossa luovuus, taito ja innovaatio yhdistyvät tuottaakseen erittäin tarkkoja osia, jotka ohjaavat toimialoja ja muokkaavat modernia maailmaa. Se on sekä taidemuoto, joka vaatii käsityötaitoa ja asiantuntemusta koneistajilta, jotka muuttavat raaka-aineita tekniikan huipputeoksiksi, että tiedettä, joka luottaa huipputeknologiaan, materiaalitieteeseen ja edistyneisiin prosesseihin saavuttaakseen vertaansa vailla olevan tarkkuuden. Tarkkuuskoneistuksen matka vie meidät materiaalien ja niiden ominaisuuksien ymmärtämisen, leikkaustyökalujen ja koneiden hallinnan sekä prosessien ja toleranssien huolellisen hallinnan kautta. Se kattaa geometrisen mitoituksen ja toleranssin kielen, tilastollisen prosessiohjauksen valppauden ja sitoutumisen laadunvarmistukseen. Tarkkuuskoneistuksella on keskeinen rooli monilla teollisuudenaloilla ilmailu- ja autoteollisuudesta lääketieteellisiin laitteisiin ja elektroniikkaan, ja se muokkaa kaikkea lentokoneiden moottoreista tekoniveliin ja mikrosiruihin. Se mahdollistaa komponenttien luomisen, jotka toimivat vertaansa vailla olevalla tarkkuudella ja luotettavuudella, usein ylittäen mahdollisuuksien rajoja.B. Viimeiset ajatukset
Kun päätämme tämän tarkkuuskoneistuksen tutkimisen, on selvää, että tällä alalla ei ole kyse vain osien luomisesta; kyse on mahdollisuuksien luomisesta. Tarkkuuden tavoittelu ajaa innovaatioita ja lyö saavutettavien rajoja. Olipa kyseessä herkkä käsityötaito, jota vaaditaan kellon monimutkaisten vaihteiden luomiseen, tai edistynyt teknologia, jota tarvitaan monimutkaisten ilmailu-avaruuskomponenttien valmistukseen, tarkkuustyöstö on kaiken ytimessä. Tarkkuuskoneistuksen tulevaisuus on täynnä lupauksia. Materiaalitieteen, automaation ja digitaalitekniikan edistys muokkaa maisemaa edelleen. Miniatyrisointi, 3D-tulostus ja kestävät valmistuskäytännöt nousevat yhä näkyvämmäksi ja tuovat alalle uusia näköaloja. Maailmassa, jossa tarkkuus on tärkeämpää kuin koskaan, tarkkuuskoneistus on edelleen nykyaikaisen suunnittelun välttämätön tukipilari. Se on osoitus ihmisen kekseliäisyydestä ja peräänantamattomasta pyrkimyksestämme huippuosaamiseen tuotannon kaikilla osa-alueilla. Kun tarkkuus ja monimutkaisempi komponentti kasvavat, tarkkuustyöstö kehittyy edelleen ja vastaa huomisen haasteisiin samalla omistautumisella ja tarkkuudella, joka on määritellyt sitä vuosisatojen ajan.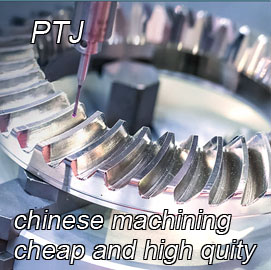
palvelumme
- 5-akselinen työstö
- CNC-jyrsintä
- CNC-kääntö
- Koneistusteollisuus
- Koneistusprosessi
- Pintakäsittely
- Metallin työstö
- Muovinen työstö
- Jauhemetallurgia muotti
- Die Casting
- Osien galleria
Tapaustutkimuksia
- Auto metalliosat
- Koneiden osat
- LED-jäähdytyslevy
- Rakennusosat
- Mobiiliosat
- Lääketieteelliset osat
- Elektroniikkaosat
- Räätälöity työstö
- polkupyörien osat
Materiaaliluettelo
- Alumiinin työstö
- Titaani koneistus
- Ruostumattoman teräksen työstö
- Kuparin työstö
- Messinkikoneistus
- Supermetalliseoskoneistus
- Kurkistus koneistus
- UHMW -koneistus
- Yksilöi koneistus
- PA6 Koneistus
- PPS -koneistus
- Teflon -koneistus
- Inconelin työstö
- Työkaluteräksen työstö
- Lisää materiaalia
Osien galleria